배터리 생산
주요 혜택
-
The TeraCota 센서는 코팅 두께, 밀도 및 하중을 고유하게 측정합니다.
-
전극 코팅(음극 및 양극)의 제조 공정을 최적화하세요.
-
이 모든 것을 실시간으로 비접촉식으로 측정할 수 있습니다.
-
용량을 개선하고 최적화하세요.
-
낭비 및 폐기되는 셀을 제거하세요.
-
제조 비용을 절감하고 관리하세요.
-
전극 코팅의 균일성을 보장합니다.
배터리 제조 산업은 가장 빠르게 성장하는 생산 산업 중 하나로, 2030년에는 연간 글로벌 리튬 이온 배터리 용량 수요가 1,000GWh 이상의 셀 에너지로 증가하여 1,500억 달러 이상의 투자가 이루어질 것으로 예상됩니다.
사양을 벗어난 셀의 폐기로 인한 리튬 이온 배터리 제조 손실은 30%에 달할 수 있으며, 새로운 제조 가동이 증가하면 그 수치는 더욱 높아질 수 있습니다.
이러한 낭비는 전체 배터리 비용에 영향을 미치며, 기가 팩토리에서 생산이 확대됨에 따라 매우 중요해집니다.
테라헤르츠 기술은 비접촉식이기 때문에 일반적으로 초음파 기술에 사용되는 물과 같은 결합 유체가 필요하지 않아 환경 친화적이며 동일한 셀에서 색상 마감과 같은 추가 측정을 평가할 수 있습니다.
전극 코팅 생산에서 코팅 두께, 밀도, 하중 및 전도도를 신속하게 모니터링하고 공정 제어를 위한 실시간 피드백을 제공하는 기능은 낭비 비용을 없애고 생산 중단 없이 시장에 공급하는 데 중요한 기여를 합니다.
전극 측정 기술은 각 파라미터를 모니터링하기 위한 여러 기술이 확립되어 있는 분야입니다. 이전에는 하나의 디바이스로 모든 주요 파라미터를 실시간으로 측정할 수 없었습니다.
샘플링 및 테스트와 같은 오프라인 기술도 사용됩니다. 그러나 대규모 생산의 경우 오프라인 시행착오 방식은 많은 추가 낭비와 장비 다운타임으로 이어질 수 있습니다.
인라인 측정은 위에서 언급한 실시간 프로세스 제어의 기회와 함께 비용 절감 및 공급 보험의 이점도 제공합니다.
테라헤르츠 기술TeraCota을 구현한 TeraView생산 현장에서 모든 주요 파라미터를 실시간으로 측정하는 단일 비접촉식 센서입니다.
테라헤르츠 기술은 매우 정확한 비행 시간 측정을 사용하여 서로 다른 코팅 인터페이스에서 테라헤르츠 펄스의 다중 반사를 기반으로 전극 두께를 결정합니다.
또한 이 솔루션은 양극과 음극에 똑같이 잘 작동하며 건식 또는 습식 전극에 모두 적용할 수 있습니다.
생산 공정에는 테라헤르츠 센서가 공정 제어에 인터페이스하여 폐기물을 줄일 수 있는 여러 단계가 있습니다(아래 그림 6 참조).
최적의 인라인 구성은 코팅 매개변수를 측정하고 이를 피드백하여 코팅 속도, 간격, 건조 등을 제어합니다.
이 솔루션은 캘린더형 및 비캘린더형 전극 모두에서 작동합니다.
일반적인 시스템에는 생산 중에 전극을 가로지르는 갠트리에 센서 헤드가 장착되어 있습니다. 갠트리의 통과 속도는 제조 요구 사항을 최적화하도록 프로그래밍할 수 있습니다. 헤드는 갠트리 메커니즘의 에너지 체인에 내장된 유연한 광 케이블을 통해 제어 캐비닛에 연결됩니다. 시스템 PC는 측정된 파형을 주요 파라미터로 변환하고 작업자가 사용할 수 있도록 이를 표시합니다.
- 양극 및 음극 모두에 적합
- 건식 및 습식 전극 측정
- 여러 전극 유형 테스트 : LFP, NMC, LTO, LMO
- +/- 1µm 정확도
- 최대 2m의 웹 너비 가능
- 양면 또는 단면 전극
전극 제조 공정의 핵심 성과 지표
배터리 제조 산업은 향후 10년간 가장 빠르게 성장하는 생산 산업 중 하나가 될 것으로 예상되며, 연간 전 세계 리튬 이온 배터리 용량 수요는 2018년 160GWh 셀 에너지에서 2030년 1000GWh 셀 에너지 이상으로 증가하여 1,000억 달러 이상의 투자와 연간 1,000억 달러 이상의 수익을 창출할 것으로 예상됩니다 [1]. 이러한 투자를 지속 가능한 비즈니스 모델로 전환하기 위해서는 내연기관 차량에 비해 전기차의 경쟁력을 확보하기 위한 비용 효율적인 배터리 제조가 전제 조건입니다. 이는 리튬 이온 배터리를 필요로 하는 다른 산업과 제품에도 동일하게 적용됩니다.
배터리 생산에서 중요한 과제는 제조 공정을 최적화하여 장기적인 사이클링 성능과 용량 수명을 개선하는 동시에 제조 비용을 절감하고 통제하는 것입니다. 배터리 팩의 최종 품질을 결정하는 생산의 핵심 단계는 음극과 양극에 사용되는 코팅의 품질과 일관성에 중점을 둔 전극 제조 공정입니다. 전극은 일반적으로 음극용 알루미늄과 양극용 구리인 집전체를 코팅하여 제조됩니다.
코팅은 일반적인 리튬 이온 양극의 리튬-니켈-마그네슘-코발트-산화물(NMC)과 음극의 흑연과 같은 활성 물질로 구성된 슬러리 혼합물입니다. 코팅에는 일반적으로 전도성 탄소 나노입자(예: 카본 블랙), 폴리머 바인더 및 용매도 포함됩니다. 그런 다음 이 혼합물은 공기 흐름, 열, 주변 압력 감소, 방사선 또는 기타 고급 건조 공정에 노출되어 건조됩니다[2]. 그런 다음 캘린더 공정을 사용하여 건조 코팅을 압축하여 다공성을 줄임으로써 전지의 에너지 밀도를 높이되, 리튬 수송 및 기타 형태의 전도를 위한 충분한 다공성을 남깁니다[3].
전극 생산 공정에는 음극 및 양극 코팅의 균질성, 품질 및 성능을 지속적으로 최적화, 모니터링 및 유지할 수 있는 여러 가지 핵심 성과 지표가 있습니다.
- 코팅의 밀도 - 배터리 셀의 에너지 밀도를 극대화하는 데 중요하지만 리튬 수송 및 기타 전도 메커니즘을 위한 충분한 다공성을 유지해야 합니다. 단위 면적당 활성 물질의 질량은 전극의 최종 용량을 결정하며, 에너지 밀도를 높이려면 코팅 중량이 높을수록 바람직하지만 일반적으로 전력 밀도도 낮아집니다. 따라서 애플리케이션에 필요한 전력 요건을 충족하면서 에너지 밀도를 최대화하려면 두 가지를 절충해야 합니다. 이러한 이유로 코팅 밀도를 구체적으로 제어하는 것이 매우 바람직합니다. 따라서 밀도는 코팅의 전기화학적 특성을 결정하는 핵심 변수입니다.
- 코팅 두께 - 생산 공정과 최종 제품에서 코팅 두께의 균일성을 보장합니다. 전극이 두꺼울수록 더 많은 양의 활성 물질이 포함되어 에너지 밀도가 높아지지만 확산 거리가 길어져 출력이 낮아질 뿐만 아니라 전극 전체에 고르지 않은 반응을 일으켜 성능 저하가 더 빨라질 수 있습니다. 따라서 이러한 효과의 균형을 맞출 수 있는 최적의 두께가 존재하며, 두께에 대한 제어가 중요합니다[2].
- 코팅의 전도성 - 전도성이 높을수록 방전 속도가 빨라지고 주어진 시간에 배터리에서 더 많은 에너지를 추출하여 용량이 향상됩니다[4].
이러한 핵심 성과 지표를 측정하는 것이 매우 유용한 생산 프로세스에는 다양한 단계가 있습니다.
- 집전체 금속 기판에 코팅이 적용된 후 코팅 건조 공정 전 또는 후의 모습. 현재 코팅 및 건조 공정만 전극 제조 총 비용의 22%를 차지하는 것으로 보고되고 있습니다[2].
- 건조 코팅이 압축되는 캘린더링 프로세스 전 또는 후입니다.
현재 사양을 벗어난 전극의 폐기로 인한 리튬 이온 배터리 제조 손실은 생산량의 2~5%에 달하며[5,6], 새로운 제조 공정이 증가하면 그 수치는 더욱 높아질 수 있습니다. 이러한 낭비는 전체 배터리 비용에 영향을 미치며, 기가 팩토리에서 생산량이 증가함에 따라 매우 중요한 문제가 됩니다.
전극 코팅 생산 시 코팅 두께, 밀도 및 전도도를 신속하게 모니터링하고 공정 제어를 위한 실시간 피드백을 제공하는 기능은 낭비 비용을 없애고 생산 중단 없이 시장에 공급하는 데 중요한 기여를 합니다.
프로세스 제어 및 피드백을 위한 측정 도구
리튬 이온 전극 제조 공정은 다양한 공정 모니터링 기법이 개발되어 있는 분야입니다. 그러나 이러한 기법들은 위에서 언급한 모든 핵심 성과 지표를 제공하지는 않으며, 종종 단독으로 사용되거나 품질 관리 수단으로 오프라인에서 사용되는 경향이 있습니다. 코팅된 전극과 코팅되지 않은 기판의 샘플링 및 무게 측정과 같은 오프라인 기법도 사용됩니다. 그러나 대규모 생산에서 오프라인 시행착오 방식은 많은 추가 낭비와 장비 다운타임을 초래할 수 있습니다[2]. 인라인 기술은 샘플 포인트를 채취하는 것보다 더 많은 코팅을 측정하며, 보다 광범위한 검사를 통해 코팅의 결함을 더 잘 감지할 수 있습니다. 또한 신속한 인라인 측정은 위에서 언급한 바와 같이 실시간 공정 제어의 기회를 제공하며, 비용 절감 및 공급 보험의 이점을 제공합니다.
현재 코팅 밀도, 두께, 전도도를 인라인에서 직접 동시에 측정할 수 있는 기술은 없습니다. 예를 들어 근적외선 파장의 레이저 삼각 측량 또는 레이저 캘리퍼를 사용하여 두께를 추정할 수 있지만[2], 불투명 코팅에서는 구현하기 어렵고 코팅되지 않은 기판에 대한 보정이 필요하고 생산 환경에서 정밀한 정렬을 유지해야 하므로 부정확한 결과를 초래할 수 있습니다. 코팅 무게를 측정할 수 있는 센서를 사용할 수 있습니다. X-선, 베타 및 감마 방사선은 투과 및 반사 지오메트리에 사용할 수 있지만 안전 문제와 정확한 신호를 수집하기 위해 긴 시간 동안 통합해야 할 필요성(베타 센서의 경우)이 모두 있습니다. 산업에서 사용되는 빠른 코팅 속도 때문에 코팅의 상당 부분을 놓칠 수 있습니다. 초음파는 코팅된 재료의 무게를 측정하는 데에도 사용할 수 있지만 안정적이고 정확한 보정이 필요합니다.
또한 위의 모든 방법에서는 원하는 성능 지표인 코팅 밀도가 아닌 코팅 중량을 측정합니다. 코팅 밀도는 계산할 수 있으므로 간접적으로 추정할 수 있지만 다른 센서 세트의 두께 측정에 의존하므로 오차가 더 커질 수 있습니다. 최적의 구성은 인라인 두께 및 코팅 밀도 측정을 위한 단일 센서입니다. 이 센서는 코팅 두께와 밀도를 실시간으로 코팅 증착 제어 프로세스(예: 생산 라인의 속도, 증착 시스템에 사용되는 간격 수정 등)에 피드백하여 코팅을 최적화하고 품질을 유지함으로써 인라인 제어를 가능하게 합니다. 지금까지는 위에서 언급한 측정 기술로는 이러한 인라인 공정이 가능하지 않았습니다.
코팅 두께, 밀도 및 전도도를 위한 테라헤르츠 펄스 기술
마이크로웨이브와 적외선 사이에서 작동하는 테라헤르츠 펄스 기술은 하나의 센서로 코팅 밀도, 두께, 전도도 등 세 가지 주요 성능을 모두 측정할 수 있는 솔루션을 제공합니다. 지난 10년 동안 테라헤르츠는 첨단 반도체 패키징[7], 자동차 생산 라인의 자동차 페인트 두께 측정[8], 자동차 부품의 인라인 코팅 두께 측정 등 다양한 산업 분야의 공정 제어 및 생산에서 확고한 검사 도구로 자리 잡았습니다. 테라헤르츠 기술은 매우 정확한 비행 시간 측정(그림 1)을 사용하여 다양한 코팅 인터페이스에서 테라헤르츠 펄스의 다중 반사를 기반으로 코팅 두께를 측정합니다. 이 기술은 비행 시간이 코팅 두께로 변환되는 고주파 펄스 레이더 시스템으로 작동합니다.
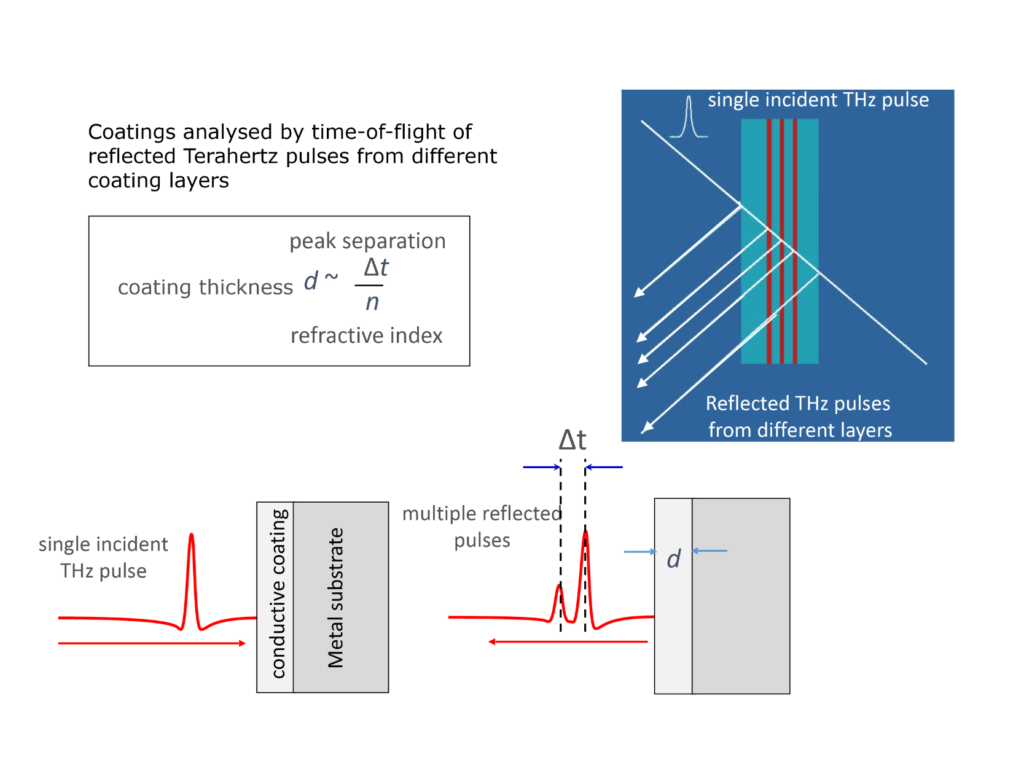
그림 1: 테라헤르츠 펄스 측정을 통해 결정된 코팅 두께.
다른 기술에 비해 테라헤르츠가 갖는 또 다른 상당한 장점은 코팅 굴절률의 실수(no)와 허수(k) 부분(n = no+ik)을 동시에 측정할 수 있다는 점입니다. 테라헤르츠 펄스의 이러한 고유한 기능은 코팅의 주요 성능 지표에 대한 중요한 정보를 제공합니다.
- 코팅의 두께: 코팅 두께 d는 c는 빛의 속도, n은 굴절률, ∆t는 코팅 인터페이스에서 나오는 테라헤르츠 펄스의 시간 지연이라는 공식을 사용하여 계산할 수 있습니다( 그림 1 참조).
- 코팅의 밀도: 테라헤르츠 단위의 재료굴절률의 실수 부분은 재료의 부피 밀도에 비례하며[9], 보정을 통해 밀도를 직접 측정하는 데 사용할 수 있습니다( 그림 2 참조).
- 코팅의 전도도: 테라헤르츠 단위의 재료 굴절률 k의 허수 부분은 σ(ω) = nockω방정식을 사용하여 고주파 전도도 σ와 관련되며, 여기서 ω는 테라헤르츠 주파수이므로 생산 공정 중에 필름의 전기적 특성을 모니터링 및 조정하거나 공정의 모델링 및 예측에 off-line으로 사용할 수 있습니다.
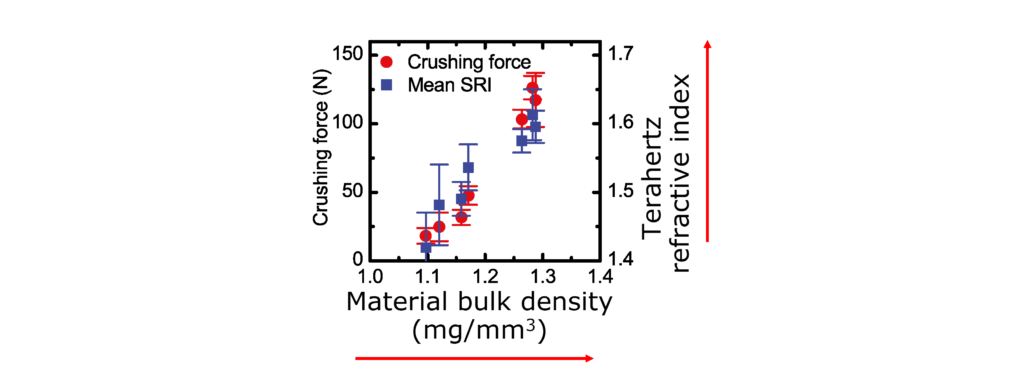
그림 2: 소재의 밀도가 테라헤르츠 굴절률에 미치는 영향 [9].
TeraView 는 독점적인 테라헤르츠 펄스 기술을 사용하여 다양한 응용 분야의 코팅을 측정을 해왔습니다. 선도적인 자동차 리튬 이온 배터리 제조업체 및 학계 업체와 협력하여 TeraView 는 이러한 기능을 배터리 전극의 코팅으로 확장하고 있습니다. 영국 내 패러데이 연구소 및 버밍엄 대학교와 협력하여 TeraView는 음극과 양극의 코팅 필름을 측정했으며, 아래 그림 3과 그림 4에 요약되어 있습니다.
그림 3은 aluminium의 NMC(리튬-니켈-망간-코발트-산화물) 기반 양극의 테라헤르츠 측정값을 보여줍니다. 테라헤르츠 측정의 광범위한 범위를 설명하기 위해 얇은 코팅(15 μm)과 두꺼운 코팅(70 μm)을 모두 조사했습니다. 테라헤르츠 파형의 쌍둥이 피크는 코팅의 전면 및 후면 인터페이스가 얼마나 쉽게 분해되고 코팅 두께가 정확하게 측정되는지 보여줍니다. 생산 시스템에서 코팅 두께의 간단한 값은 작업자 또는 공장 데이터 관리 시스템으로 자동 반환됩니다. 양극 폭에 걸쳐 테라헤르츠 센서를 스캔하면 표면 및 표면 아래 코팅 프로파일은 물론 양극 전체에 걸친 코팅 두께 자체의 선형 플롯이 표시됩니다. (아래 그림 3c 참조).
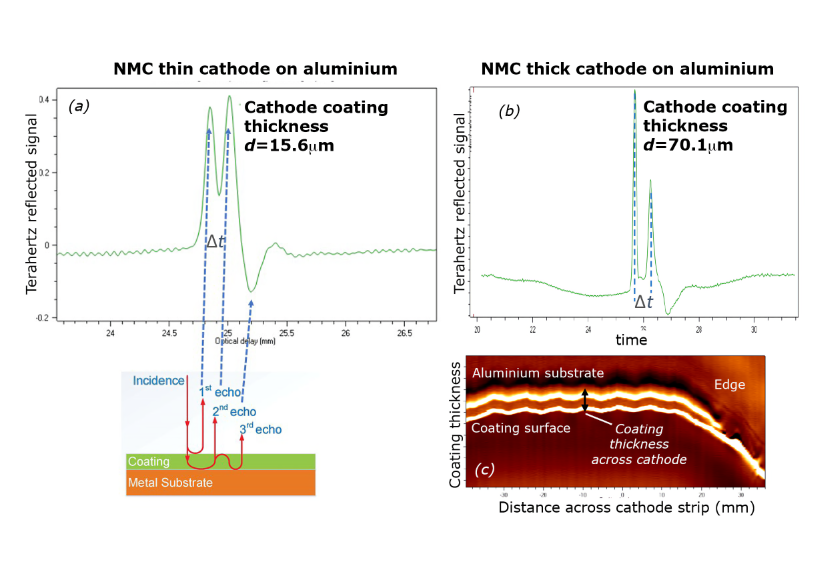
그림 3: 양극 - 테라헤르츠 측정: aluminium에 NMC 코팅 (a) 얇은 코팅, (b) 두꺼운 코팅, (c) 양극 전반의 코팅 두께 단면 이미지로, 리튬 이온 배터리에 사용되는 양극 전반의 두께를 측정하고 매핑하는 테라헤르츠의 능력을 보여줍니다.
그림 4는 copper에 carbon black과 binder를 혼합한 graphite을 기반으로 한 음극 코팅의 테라헤르츠 측정값을 보여줍니다. Graphite은 테라헤르츠를 더 많이 흡수하지만 테라헤르츠 파형에서 두 개의 피크가 분리되어 코팅의 전면 및 후면 인터페이스를 식별하고 코팅 두께를 정확하게 측정합니다. 이 기술은 더 두꺼운 음극 코팅에서도 입증되었으며, 다른 코팅 생산 분야에서 graphite 층을 측정한 TeraView 의 수년간의 경험을 바탕으로 합니다.
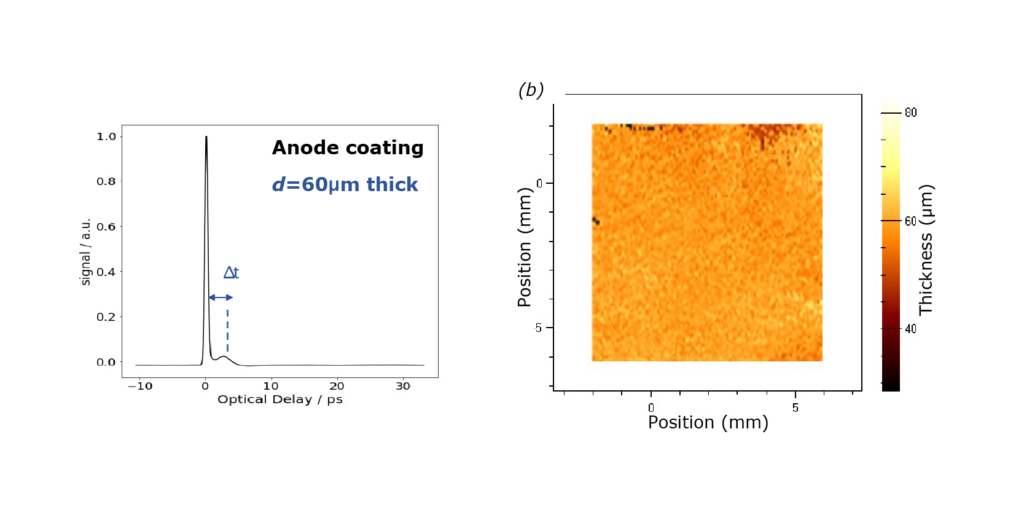
그림 4: 음극 - 테라헤르츠 측정: copper에 grahpite 코팅 (a) 코팅의 표면과 코팅 뒷면에서 반사되는 파형과 60 mm의 두께를 보여주는 파형 (b) 8 mmx8 mm 음극 필름에 대한 층 두께의 분포.
생산 공정에서 코팅 공정 제어를 위한 피드백
TeraView의 제품은 코팅 측정이 공정 품질 및 공정 관리의 핵심이며 제품 공급을 유지하는 것이 필수적인 다양한 산업 분야의 생산 응용 분야에서 확립된 실적을 보유하고 있습니다.
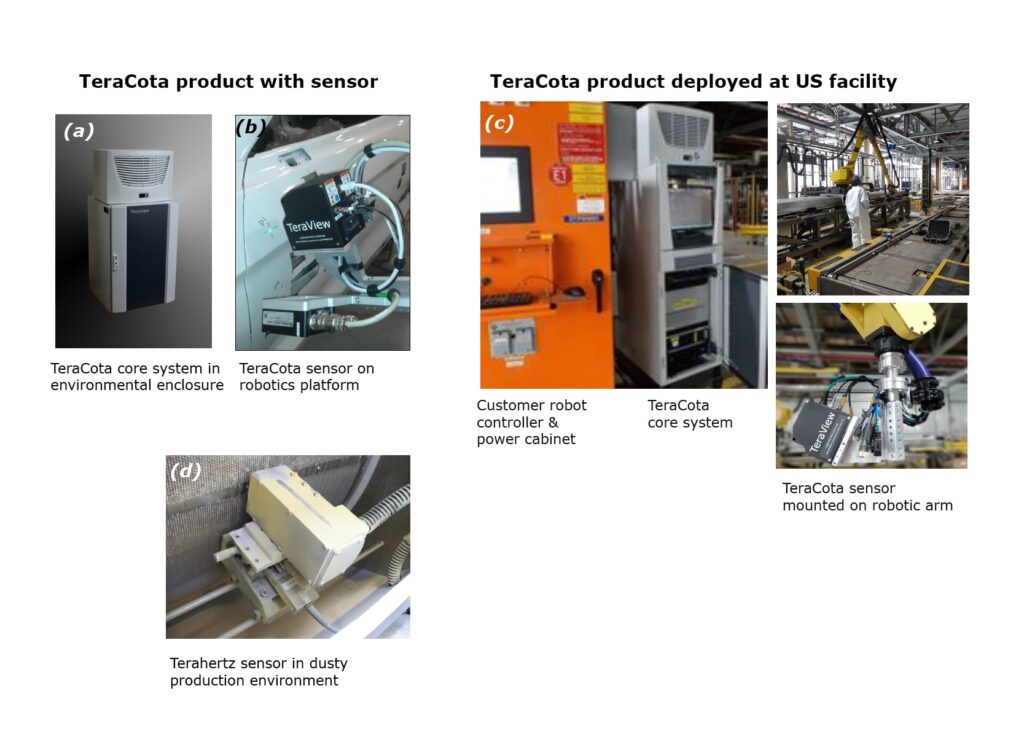
그림 5: 생산 라인 내 TeraCota 코팅 측정 시스템: (a) TeraCota의 core 시스템, (b) Umbilical 케이블을 통해 원격 엑세스가 가능한 TeraCota 센서, (c) 시스템, 센서 및 자동화(로봇) 플랫폼을 보여주는 미국 자동차 생산 시설 환경, (d) 먼지가 많은 산업 환경에서도 사용되는 TeraCota 센서.
TeraView의 TeraCota 제품(그림 5a 및 5b)은 유럽, 미국, 아시아의 자동차 생산 공장에 배치되어 코팅을 측정하고 있습니다. 예를 들어, 미국의 한 대형 시설에 구축된 사례는 그림 5c 에 나와 있습니다. 이러한 설치에는 진동, 온도 변화 등 생산 환경과 관련된 여러 가지 문제를 해결하는 것이 포함되었습니다. 데이터의 재현성과 정확성은 광범위하게 입증되었습니다. TeraView의 센서 헤드는 먼지가 많은 환경에서도 사용할 수 있도록 설계되었습니다. (예: 그림 5d)
양극과 음극의 생산 공정에는 테라헤르츠 센서가 공정 제어 및 비용 절감에 역할을 할 수 있는 여러 단계가 있습니다. (아래 그림 6 참조) 최적의 생산 라인 구성은 코팅 두께와 밀도를 측정하고 이러한 파라미터를 피드백하여 코팅 속도와 간격을 제어할 수 있습니다. 건조 전과 후에 이러한 측정을 수행하여 추가 정보를 획득할 수 있습니다. 습식 두께와 적용된 간격을 비교하면 공정의 탄성에 대한 정보를 얻을 수 있습니다.
테라헤르츠가 측정하는 건식 코팅 밀도와 두께는 코팅의 에너지 및 전력 용량을 결정하므로 코팅 생산의 간격과 속도를 변경하여 최적화할 수 있는 궁극적인 요소가 됩니다. 두께, 밀도 및 전도도를 동시에 실시간으로 측정하는 TeraView의 고유한 솔루션을 사용하면 이러한 생산 매개변수에 대한 피드백 및 제어를 통해 고객 요구 사항에 맞게 조정할 수 있습니다.
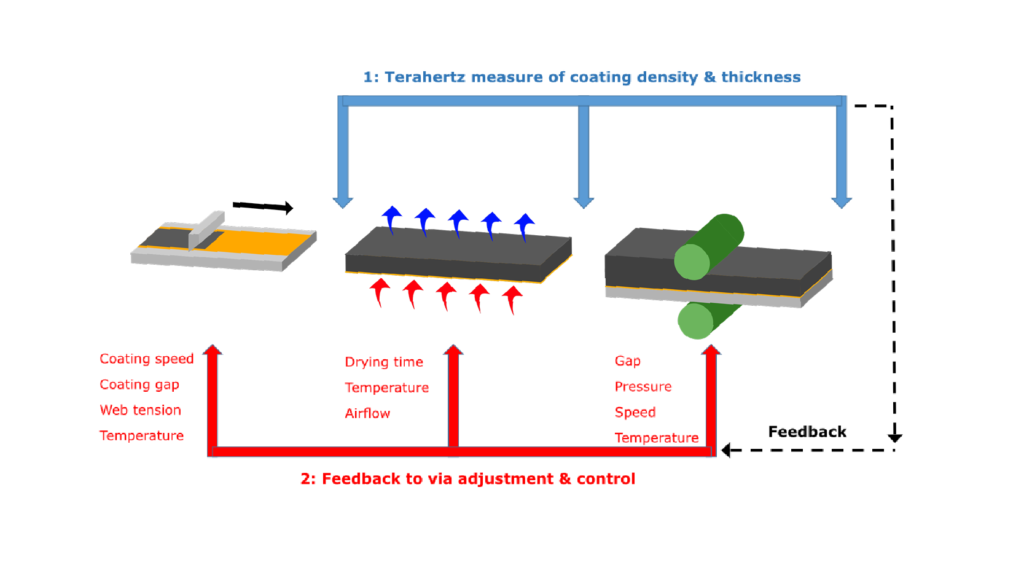
그림 6: 전극 코팅 생산의 주요 단계 및 파라미터, 공정의 여러 부분에서 테라헤르츠 센서로 측정한 코팅 두께와 밀도를 사용하여 생산의 피드백 제어[3].
참조
- Avicenne Energy, 2019.
- Materials & Design 209 (2021) 109971.
- Journal of Power Sources 393 (2018) 177-185.
- https://undergraduateresearch.virginia.edu/investigating-conductivity-lithium-ion-batteries-across-porous-thin-films-through-manipulation-0.
- Journal of Minerals, Materials and Metals 69 (2017) 1484– 1496.
- Int. J. Prod. 232 (2021) 107982.
- ‘Localization and Characterization of Defects for Advanced Packaging Using Novel EOTPR Probing Approach and Simulation‘, NVIDIA Corporation, Proceedings of the ISTFA Conference 2020 (2020).
- ‘Use of Terahertz-Based Sensing to Quantify Layer Thickness in Automotive Paint Systems ‘, M Nichols & T Misovski, Ford Motor Company, Proceedings of the SAE Conference April 2022 (2022).
- Journal of Pharmaceutical Sciences On-line DOI 10.1002/jps.23560 (2013).